Repairing the Transom of my Cobra Terminator
Since
my 30ft
Cobra Terminator offshore racing hull was setup for a
Bravo One outdrive, I needed to patch the transom.
Skagit
Valley College has an award winning Marine
Maintenance Technology Department as part of the Northwest
Center of Excellence for Marine Manufacturing and Technology.
I took the Vacuum
Infused Plastics (VIP) Course so I could master the skills
I need to apply the Vacuum Infusion Process to properly repair
the composite hull of my Kevlar
racing cat.
 |
Here's
a completed, composite part (still curing inside the
vacuum bag) that was fabricated during our first week
in class using the Vacuum Infusion Process. This particular
part was fed in the center and vented on both ends.
Here
you can see the resin being pushed through the cloth
material of another part (being fed from the right and
vented on the left). The open weave on this material
is fairly porous, so the resin flowed quickly.
|
 |
Here's
something you don't see very often.
 |
The
bright pattern on these two projects is actually cloth
material (like you'd buy at the fabric store for sewing
a dress) showing through the Gelcoat.
It's
pretty simple to do; using the 'open mold' process,
clear gelcoat is sprayed into the mold, then colored
cloth (fabric) is laid out with the pattern showing
the way you want. The remainder of the fiberglass is
added on top just like you would on any other fiberglass
layup. The result is a very durable, colorful pattern
on your project. Pretty slick.
|
 |
Now
that I've completed a few simple projects using the Vacuum
Infusion Process, I'm ready to use my newly acquired skills
to patch my transom where the removal of the Bravo One Outdrive
left a nice big hole. When I'm finished I'll have a 'blank'
transom (stronger than the original) to which I can mount
my ASD8 Arneson Surface Drive.
Here's
some highlights of the composite repair process of my transom.
 |
The
transom was originally constructed with two layers of
3/4" marine plywood sandwiched in vinylester resin
with E-glass; four layers of Kevlar in a 3/8" layer
of glass on the outside, two layers of Kevlar in a 1/4"
layer of glass on the inside.
The
outdrive hole repair is critical (must have no imperfections)
as this is where the Arneson ASD-8 surface drive will
mount. The few small holes are cosmetic and should be easy to patch.
|
 |
 |
After
laying out the width of my overlap and taper, I used
my skilsaw to cut through the Kevlar reinforced 3/8"
thick vinylester outer layer. With sparks flying and
Kevlar 'fuzz' all over, It's finally done.
The
outer layer of glass has now been removed.
|
 |
 |
All
the wood of the outer layer has been removed and edge
beveled (to further lock the wood patch in place). A
taper was ground on the outer layer of glass so the
resin will adhere and I can gradually increase the size
of the new cloth layers in the patch.
The
old outdrive holes have been filled and the edges evened
up (so it will be easier to fit the inside wood plug).
On the right you can see the edges of the Kevlar cloth
layers.
|
 |
 |
Here,
the outside plywood 'sandwich' plug has been fitted.
The saw kerfs allow the resin to flow through to all
parts of the repair. I ended up with 8 layers of Kevlar
cloth alternating with layers of Continuous Strand Fiberglass
Cloth (C-Glass) over this plywood plug to bring the
surface of the repair out flush and even with the face
of the original transom.
We
want the outside of the transom to be flat (as well
as smooth) so we use a sheet of Plexiglas under the
vacuum bag, with a layer of peel-ply under, so it will
not stick to the repair. A straight edge across the
Plexiglas verifies it's flat and even with the existing
transom when vacuum is applied. With the Vacuum Bag
fitted, we're ready to infuse from the bottom and vent
across the top. Several rows of holes have been drilled
under the fill area to allow the resin to pass through
the Plexiglas into the repair area.
|
 |
 |
The
outside has now been infused. For this particular application
the ability to bond to the existing resin and raw strength
were imperative. With those requirements in mind, we
selected the Epoxical
Epoxy Resin System as it is designed specifically
for this type of Infusion. The Epoxical 4310A Resin
when used with the 9235B Catalyst has a rated tensile
strength (modulus) of 427,000 psi. Perfect to handle
the stresses produced when my Arneson ASD8 Surface Drive
is hanging on the transom with 1400 HP pumping through
it.
Now
we have a flat surface that we can work with. After
some minor filling and sanding, I'll get a finish coat
applied. I'll likely use a 2-part Polyurethane paint
as this will be compatible with my graphics (to be applied
later) and minor dings are easily touched up in the
future.
|
 |
Now
we'll show the inside. I actually infused both sides at once,
but show them separately here for clarity.
 |
A
plywood sandwich has also been cut to fit the inside
(with all seams beveled and staggered).
|
 |
 |
The
holes were drilled to allow all the air to escape. Next,
the material (fiberglass cloth and Kevlar cloth) will
be dry fitted on the inside.
At
this point we have three layers of "C-Glass"
(Continuous Strand Fiberglass Cloth) alternating with
Kevlar Cloth gradually increasing in size (the top layer
of Kevlar cloth is visible) plus one full size layer
of C-Glass over the entire repair area.
|
 |
 |
A
full size layer of Kevlar cloth goes on for additional
strength. The inside repair ended up with 4 layers of
Kevlar (literally bulletproof).
Followed
by a finish layer. Now the inside of the transom is
'dry stacked' and ready for the vacuum bag.
|
 |
 |
Using
the Vacuum Infusion Process, we will be venting across
the top and filling from the bottom.
Here's
the inside repair after infusion. The repair went smoothly
and I'm very satisfied with the results.
|
 |
 |
This
close-up shows an individual patch being vented from
the outside.
And
here's the same patch being filled from the inside.
|
 |
The
whole idea is to have an 'undetectable repair' (stronger than
original) when we're finished and I'm confident I'll achieve
that goal.
After some filling and board sanding, I'll shoot it with polyurethane
paint and the repair will not only be undetectable, it will
be stronger than original.
 |
I
also fabricated a transom wedge for my ASD-8 Surface
Drive by dry stacking, then infusing a piece of carbon
fiber on the table.
Next
I sealed the cut edges with epoxy resin filler, sanded,
primed, and topcoated.
|
 |
 |
This
adapter will allow my Arneson
ASD8 surface drive to be mounted at the proper angle
to fit the transom of my 30 foot Cobra Terminator.
After
primer and topcoat it's ready to install.
|
 |
My
recent experience of attending the Vacuum
Infused Plastics (VIP) Course at the Skagit
Valley College Marine Maintenance Technology department
was quite enjoyable. I find the curriculum to be well written,
the work area nicely equipped, and the instructors are very
knowledgeable (and patient). Whether you just want to take
a single class (to gain some new boat maintenance skills like
I did), need to acquire some new skills with a one year Certificate,
or are retraining for a career change (seeking a two year
Associates Degree), the Skagit Valley College Marine
Maintenance Technology program is highly recommended.
Let's take a 10 minute break. Class dismissed.
Applying the topcoat to my Cobra Terminator
 |
Easy
to mix and apply, working with 3M
Glass Bubbles is a lot like frosting a cake. Applied
with a putty knife or drywall trowel it is about the
consistency of peanut butter. After it sets (just over
24 hours at 75° F), I board sand it flat, check with
a straight edge, and repeat as required. Then we'll
prime (with epoxy primer) and finish with a two-part
Polyurethane topcoat.
I
selected AwlGrip
2 Polyurethane topside paint for its exceptional
quality and durability. Awlgrip II is a true polyester
resin based urethane coating making it harder and much
more resistant to the environment than acrylic urethanes.
It has excellent gloss retention, resists color fade
over many years with minimal maintenance. For these
reasons it is the preference of all the mega yacht builders.
It can be wiped with harsh solvents (like acetone) without
harming the shine. The engine compartment, interior
and bilge will be Majestic Blue (Arrow 1), the hull
exterior will be Sun Yellow (Arrow 2), and the accents
will be Federal Yellow (Arrow 3). I'll also add some
stripes and shadows (in complimenting colors) to bring
it all together.
|
 |
I've
removed the rub rail as it was leaking and overall was in
pretty sad shape. I really like the 'clean look' of several
other boats I've seen that were finished without a rub rail,
so I've decided to go that route. The deck has already been
completely glassed to the hull on the inside, so all I've
got to do is cosmetic work by filling the outside seam and
old holes left from the rub rail.
 |
Here's
a close-up of where the rub rail was. In these photos
I've drilled out the rivets and ground away the loose
paint to prepare for filling. Epoxy resin mixed with
3M Glass Bubbles weighs only a few grams per batch,
yet is extremely strong; perfect for filling the imperfections
in my hull. I look forward to the 'clean look' this
boat will have without it. It will be a lot of work,
but I think it will be worth it. Ask me when it's done
if it was worth the effort.
The
rub rail provides a little protection if you tie up
against a piling or pier, but that's NOT the way I moor
my boats. From what I've seen in the Boat Building Industry,
it's just a cheap way for boat builders to quickly hide
the raw edge where the deck meets the hull. The finished
deck seam is an available option on the Eliminator
Daytona I was looking at. As I recall it added several
grand to the cost of the boat.
|
 |
 |
Here's
the rub rail area after it's been filled. I'll board
sand it flat then fill any remaining imperfections.
Then we'll use the D/A sander to blend into the contours
of the sides and deck. It will look like the 'smooth
side' option was ordered from the factory by the time
I'm done. That hole is where the Starboard navigation
light mounts (note the aircraft grade honeycomb inside
the decking).
More
to follow.
|
 |
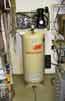 |
My
old air compressor was complaining about all the air
used by my board sander, so I installed a new Ingersoll
Rand SS5L5 vertical air compressor that cranks out
18 SCFM at 90 psi and boasts a 100% duty cycle. Now
my sanders rip!
My
air supply line runs from the compressor (in the shop),
underground across the backyard, into the boathouse
feeding a water separator. As a result, I have no noticeable
water in the line at my air tools hose reel. Since Polyurethane
paint has no tolerance for moisture, a second hose reel
(used exclusively for painting) is fed through a Deliquescent
dryer to ensure my Devilbiss
Finishline III HVLP Master Kit paint gun gets the
required volume of dry air.
|
 |
I
shopped online and got a great deal on marine paint. For the
primer, I selected PPG DP48LF 2-part epoxy primer. For the
topcoat, we'll use AwlGrip 2 in 'Sun Yellow' color. This extremely
durable 2-part Polyurethane topcoat is used throughout the
marine and aerospace industry for high end topcoat applications
subjected to extreme environments. The AwlGrip 'Sun Yellow'
is a custom color that was batch mixed specifically for the
logo of a major airline. The clear-coat will be Desothane
HS BAC 900 Gloss Clear also by PPG.
My
new DeVilbiss
FinishLine 3 HVLP Spray Paint Gun Master Kit comes with
an assortment of tips that allows me to spray the primer,
topcoat as well as the clear-coat properly, without buying
several spray guns. Since Polyurethane is extremely toxic
(even in small amounts) I'll use my new HobbyAir pressurized
air supply while painting.
Reworking the bottom of my Kevlar Cat
I
tipped my Kevlar hull up on its side so I can rework the bottom.
 |
With
a couple 6,000 lb. straps, it's an easy lift for my
overhead hoists. That's 3/8" steel in those monster
overhead I-beams and this Cobra Terminator (weighing
in at 2,455 lbs.) causes no noticeable deflection. These
I-beams came out of a local shopping mall where they
supported the roof over an ice skating rink (with a
clear-span of close to 100 feet).
Lowering
the two chain falls tip the hull onto its side. The
hoist trolleys roll freely so I'm able to shove the
hull over to the other side of the work area. Real slick.
|
 |
 |
I trimmed Styrofoam blocks to fit the side contour and
provide support (at the bulkheads) so I could balance
the hull on its side. A brace across the transom, clamped
to the overhead I beam ensures the hull will remain
steady while I work the bottom.
A
2 by 6 plank bolted into the port bow cleat hole (then
braced against the wall) also helps hold the hull steady
while I wrap up the sanding.
|
 |
I
ensured all the gunk was removed by scrubbing the entire bottom
with scotchbrite and denatured alcohol. I ground out all the
cracks, scratches, and gouges then patched with Epoxical
Epoxy Resin mixed with 3M
Glass Bubbles. It's real nice to be able to crank the
heat in my boathouse to 75° during the epoxy cure. I board
sanded all patches flat, then D/A sanded with 150 and 240
then wiped with a 'tack rag'.
I
shot a 'test batch' of primer on a scrap of fiberglass so
I could adjust my Devilbiss
Finishline III HVLP paint gun and test my materials. After
the paint set I did my own 'destructive test' and I am very
satisfied with the results. It does not scrape, chip, or gouge
off. The only way I could remove it was to actually damage
the fiberglass surface. Extremely durable!
 |
My
entire boathouse has been cleaned and the hull is masked
off. These high performance aircraft finishes are very
durable, but highly toxic; a pressurized breathing supply
(such as HobbyAir) must be used.
Now
the bottom has a fresh coat of PPG DP48LF white epoxy primer on it. I really like my Devilbiss
Finishline III HVLP paint gun; it applies a nice
even coat with minimal over spray and the DP48LF completely
hides all dark colors. We're almost ready for some color.
|
 |
 |
I
split my one gallon kits of AwlGrip polyurethane topcoat
into two equal parts (by weight) so I'd have smaller
mixed batches and plenty of time to spray. Focusing
on technique, I don't want to feel 'rushed' worrying
about the 'pot life'. There's definitely a trick to
successfully applying polyurethane topcoat and the 'flash
time' is absolutely critical.
After
applying three of the half-gallon kits of AwlGrip, the
bottom is done. I don't see why they call it 'sun yellow'
as it's more like a 'neon golden orange' when applied
over white primer. But whatever you call it, the color
is really beautiful and I'm happy with the results. Calling it 'paint'
does not do it justice.
|
 |
Reworking the sides and deck of my Kevlar
Cat
Now
that the bottom is all done I can get busy on the rest of
the hull.
 |
After
letting it set for the required 14 days cure time (at 75°),
I rolled the hull over level and set it back on the trailer.
I was able to shape
the rails with my board sander. A few more batches of
filler and it should be done.
|
 |
In
addition to getting the remaining filling and sanding done
on the sides, rubrail, and deck
a couple modifications
are in work to 'personalize' my Kevlar Offshore Racing Cat.
 |
I'm
moving the 'signature' Cobra Terminator deck hatches
further forward. The new location will facilitate easy
access to the forward cleats. Instead of climbing up
and over the (sometimes slippery) deck, my helper can
go below decks, pop the hatch open, and easily attach
a mooring line (and bumper) to either bow cleat. Real
slick.
To
fabricate patch material for the old hatch cutouts,
I sandwiched honeycomb composite board and Kevlar cloth
between layers of Chopped Strand cloth.
|
 |
 |
The
stack is now laminated with epoxy resin and is ready
to clamp.
We'll
let it set on a flat surface with a plate and a little
weight on top.
|
 |
 |
A
layer of tin foil prevented the epoxy from sticking
to everything and peels off easily.
I
suspended the plug over the hole, sealed the underside
of the joint with duct tape, and applied epoxy into
the seam (with chopped strand cloth soaked in resin).
|
 |
 |
Epoxy
mixed with a little Cab-o-Sil
fills what's left of the seam. Next, I'll feather the
edge out using Epoxy Resin mixed with filler and board
sand flat.
For
the last coat of filler I tried something new. This
time I filled the low spots with West
Systems 407 Low-Density filler (brown color). It
mixes much the same as 3M
Glass Bubbles (the white color filler), but seems
to stay 'wet' as you mix it thicker (unlike 3M Glass
Bubbles which tends to 'dry out' the more you mix in).
|
 |
 |
Not
only is this repair strong and light, it will be undetectable.
More to follow.
|
 |
I
took the time to move my controls over to the right. All my
other boats have been right-hand drive, and I feel more comfortable
over there.
 |
I
trimmed the bottom edge of the dash board back to provide
more legroom and filled the bottom (exposed) edge of
the end-grain balsa dash board and radiused all the
edges.
I
glassed in some composite panels to form a small storage
area along the sides of the cockpit. Now each passenger
will have a safe place to stow small items while underway.
|
 |
 |
PPG
DP48LF white epoxy primer will provide a good solid
base on which to apply the topcoat.
The
primer covers all the shadows so when we apply the AwlGrip
2-part polyurethane 'Sun Yellow' it will provide an
even color.
|
 |
 |
Finally,
the topsides are all ready for primer.
I
started with a white hull, so my eyes are telling me
I'm back where I started. But my mind knows better.
All the defects have been properly repaired and we're
almost ready for the final topcoat finish.
|
 |
 |
When
working with composites, sometimes there is a problem
with pinholes showing through the primer. To correct
this I'm trying some Akzo
Nobel 28C1 Composite Pinhole Filler.
This
single part Composite Filler looks like mayonnaise and
is applied with a rag. Now my epoxy primer adheres evenly.
|
 |
Now
the topsides are all primered.
 |
Next
we'll sand with 400, clean the boathouse, wipe down,
mask off, and shoot the AwlGrip polyurethane topcoat.
Now
she has an extremely durable 'sun yellow' polyurethane
topcoat.
|
 |
 |
I
shot some blue graphics on the sides and down the centerline
of the deck.
I'm
very satisfied with the way the rub-rail turned out.
|
 |
 |
The
AwlGrip 'Majestic Blue' is a nice contrast to the 'Sun
Yellow' background.
I
got the Clear Coat applied. Next, I'll add some 'Federal
Yellow' graphics and black non-skid on the topside fore
deck (down the centerline form the bow to the cockpit).
More to follow.
|
 |
I've
gathered several AwlGrip
2 Polyurethane colors for my custom stripes including;
Majestic Blue, Teal Blue, Vivid Red, Jet Black, Federal Yellow,
and Medium Gray.
Then I'll top it off with three layers of clear-coat and may
even mix in some Shimmer
Orange Copper Candy Pearl for a 'custom look' (if I can
learn how to shoot pearl).
I'm
taking a break from painting so I can begin the mechanical
work. Once all my brackets are infused in place, I'll get
the paint out again to shoot the bilge and add a few more
graphics.
Now
I'll focus on getting the drive train installed
 |
Here
I began the process of 'dry fitting' my ASD8 Arneson
Surface drive. My transom turned out so nice, I really
hated to drill into it.
Now
it's beginning to look like a race boat once again.
After the clear coat has been applied, I'll permanently
mount my surface drive. Yes, I'll flip the steering
cylinder over.
|
 |
 |
I
finally got my Arneson
ASD8 surface drive mounted. Wet set with a tube
of 3M 5200 caulking, it's not going anywhere.
Next,
I'll set the gas turbine in place and measure the drive
line
|
 |
 |
Once
I get hydraulics hooked up, the trim cylinder will hold
the drive up in the position for running.
Once
I get the drive line fabricated, I'll locate the engine
and design motor mounts.
|
 |
Now
that we have our drive line fabricated we get to work with
composites again.
 |
When
the engine was set in place I identified the gearbox
and engine support bracket locations and cut cardboard
templates. A metal bracket will be mounted on the horizontal
'flat spot' for the gearbox 'ear' to bolt through.
I
cut some material off my sheet of Carbon Fiber to form
the outline of the brackets.
|
 |
 |
Marine
plywood sandwiched in carbon fiber will become the motor
mounts.
The
surface of the existing fiberglass is 'scuffed' to ensure
a good bond.
|
 |
 |
I
need to reduce the height of the center stringer (to
clear the underside of the gas turbine), so I reinforced
it first with Carbon Fiber. Shell 828 Epoxy Resin was
selected for its exceptional secondary bond and brute
strength.
A strap anchored to a pair of carbon fiber 'keepers'
will securely hold each battery in place.
|
 |
 |
I
used carbon fiber brackets to mount my dry sump oil
tank to the transom.
I'll add sight gauges so I can see my oil level at a
glance.
|
 |
The composite motor mounts are now laminated in place (with
overlapping layers Kevlar and 'C-Glass').
See
the installation of my 1400
HP monster gas turbine
Now that many of my components are 'dry fitted', it's time
to fabricate the engine cover
 |
After
trying several different designs and locations, I finally
settled on a pair of Aero Scoops from top fuel funny
cars. Mounted forward, they will bring fresh air in
under the floor and into the engine compartment.
I
performed 'major surgery' to enlarge each one so they
will scoop in an adequate supply of fresh air. Here
the sides have been cut, enlarged by 3", paneling
screwed in place as a form, and glassed in. Kevlar cloth
and epoxy resin is used to keep them light and strong.
|
 |
 |
Here
the lip of the mouth has been formed with Epocast Composite
Filler. This pair of scoops will bring in about 45%
more air than is required for combustion to ensure the
engine compartment is properly cooled.
A
pair of thermostatically controlled electric fans will
keep the air moving and temperatures under control (even
when tied up to the dock after a high-speed run). Here
the sides have been filled with a layer of Epoxy Resin
mixed with 3M Glass Bubbles. More to follow.
|
 |
Besides
being all 'butchered up', the original hatch cover was poorly
fitted and in sad shape. So I started from scratch, designing
a new one out of composites.
 |
For the deck lid of the engine cover I selected Aerocell
ASP404 1/2" composite honeycomb board for its light
weight and exceptional strength (seen here rough cut
with the proper arch applied).
Now
the rear bulkheads are beginning to take shape. Cut
from 1/4" aircraft grade aluminum honeycomb board,
the bulkheads are bolted to honeycomb composite board
which is 'tabbed' to the deck and side of the hull.
|
 |
 |
Here,
I used Huntsman
Epocast 87005 2-part 'edge sealer' to seal the exposed
edge of the honeycomb board. I borrowed my wife's Tupperware
bowl and shortening cutter since it's a lot like mixing
cookie dough.
I lined the hatch rail with a layer of cardboard (duct
taped in place) so I can use it as a mold. I applied
edge sealer to capture the shape of the hatch lip.
|
 |
 |
In
this view (underside of the hatch cover) you can see
the edge sealer in place. I've removed the hatch deck
from the mold and sanded. The cardboard reduced the
size enough to allow me to add a couple layers of fiberglass
and still fit properly .
This
rib will provide support across the underside of the
hatch. It's laid out in a curve to go around the future
exhaust cutout.
|
 |
 |
The
support rib foam is bevel cut and ready to be glassed
in.
The radius on the front lip was formed with Epocast
edge sealer. The front lip forms a seal by overlapping
the bulkhead and will open with the engine cover.
|
 |
 |
I've
applied the first layer of epoxy resin and Kevlar cloth
over the foam rib. After the Epocast sets for 48 hours
on the front lip, I'll sand a nice radius.
Here
the hatch is in place and the layout of the forward
engine cover has begun.
|
 |
 |
Next
I'll radius all the outside corners. An elastic
band pouch will go across the front after paint.
Here's
a trick to help shape the radius of the outside corners:
with a layer of 'Saran Wrap' over the Epocast edge filler,
I use a piece of PVC pipe to push on the filler and
form the rounded edge.
|
 |
 |
I
finally have the cover on over the engine and a rough
cut around the exhaust.
The
cutout is trimmed and reinforced with foam board.
|
 |
Since
the Epoxical 4310A Resin worked so well for my Vacuum Infusion
projects, I looked for other Epoxical Epoxy Resin products
for the remaining laminating jobs. After a some research,
I located a source for Epoxical
574 Epoxy Resin for laminating the engine cover.
 |
Here
you can see the carbon fiber mounts for my Dana
Power Hinges. A pair of quick disconnect pins will allow easy
removal of the hatch for engine removal and maintenance.
Once the Epocast Edge Filler sets (around the exhaust
cutout), I'll sand and get ready to add a layer of fiberglass.
Here
the last section of Kevlar cloth has been applied on
the inside. After the epoxy resin sets, I'll trim the
edges and start on the outside.
|
 |
 |
Here
I'm laminating the top layer of Kevlar Cloth in place
with Epoxical Epoxy Resin. This photo also shows another
neat trick: I use plastic wrap to hold the edges of
the cloth down until the resin sets.
Here
I have all the exterior Kevlar Cloth in place and I've
begun the process of filling. I use 3M Glass Bubbles
mixed in my Epoxy Resin for filler, then board sand
flat. I also mix in a little West
Systems 407 Low Density Filler to alter the color
(so it's easier to see each successive layer of filler).
|
 |
 |
The
rear deck lid is now very rigid, yet light weight. In fact,
the entire new engine cover weighs considerably less than
the old (stock) engine hatch alone. A
coat of white PPG
DP48LF white epoxy primer provides an even base
for the topcoat.
Three
coats of AwlGrip Sun Yellow two-part polyurethane really
brightens up my parts.
|
 |
Now
that the scoops are mounted, the air intake system is
now complete.
|  |
The
scoops not only bring in air for the gas turbine, but
also for cooling the engine compartment (ducted under
the floor).
|
Next,
we'll get the forward hatches assembled and installed.
 |
It's
a nice fit and finally looks like it belongs. Next,
I'll mask it off for the blue stripe and fit the stainless
steel collar (heat shield) around the exhaust.
After
a couple coats of AwlGrip Majestic Blue and a little
clear coat, the engine cover and instrument panel are
done.
|
 |
Now
it's time to add some acoustic insulation to help reduce the
turbine noise. After reading a lot of product reviews and
car audio forums, I selected Second
Skin Audio Products.
 |
The
first step was to cover the inside with a layer of Damplifier
Pro. Just trim with scissors, peel the back, and
rub it in place with a roller.
Next,
a layer of Over
Kill Pro goes on with contact cement.
|
 |
 |
Finally,
a layer of Motor
Mat Pro is installed with contact cement. The seams
and edges are cleaned up with foil tape. The two engine
bulkheads received the same treatment. This will reduce
engine noise substantially.
Next,
a strip of black nonskid paint will be applied down
the centerline of the fore deck and the front hatches
will be installed.
|
 |
A
cradle supports the engine cover when not installed.
|  |
Quick
disconnects allow easy removal for maintenance.
|
See
my progress installing
components in the engine bay.
My
turbine
powered boat is now complete.
By
the time I'm done I'll have 'gone through' every part of this
boat.
At 125 mph safety is paramount, and dependability is critical.
|