I
needed a storage building so I could get my Cobra Terminator
inside to rework the hull
Although
not actually part of my boat project, this Boathouse definitely
contributed toward my overall goal. It took me a year, but
was well worth the effort.
Now that this boathouse is complete, I'm focusing my efforts
on converting
my boat to turbine power.
I'm
able to 'shoehorn' a 26' wide by 44' long by 16' high pole
building into the back corner on my property. I designed the
building with high ceilings so I can install a 14 foot roll-up
door to get my boat inside plus my RV alongside. I'll use the additional
storage space to setup my pallet racks down the length of
one wall.
I
find the building permit application process very frustrating.
Each time I talk to the 'officials' at the local Building
Department I get a different story- they act like they've
never done this before. The building Inspector tells me I
don't need 'engineering' for a pole building. I turn in my
application and they ask "Where's the engineering"?
I found out later the local building code changed well over
a year before (now requires engineering for all pole buildings).
Not a good sign. I learned very early in my Aviation Maintenance
career, the sign of a true professional is one who does not
attempt to memorize the regulations or procedures, but knows
where to look up the answer. Then, when the procedure gets
updated or is changed, the old 'memorized' steps are not followed
(in error).
Gaining access from the street
 |
To
gain access to that back corner, I first constructed
a 'drive through' gate supported by two brick columns.
I dug down over five feet, then pounded in a four inch
steel pipe (as far as I could), then poured a solid
concrete footing around it. I laid bricks around the
steel pipe, filled the center with concrete, cut off
the top of the pipe, and topped it off with a precast
concrete cap. Integrated, heavy steel hinges provide
support for the gates. I welded some scrap 2" galvanized
pipe to form the gate frames, then attached cedar boards
to the front to match the rest of the fence. A removable
center post provides support and a method for locking
the gates while in the closed position. An adjustable
handle supports and locks each gate while open (prevents
the wind from swinging them around while I'm trying
to drive through).
|
 |
 |
For the 'driving surface' I used a product called turfstone
which installs a lot like pavers.
Turfstone bricks sit on a layer of compacted, crushed
rock (covered with a layer of sand, then grass grows
up through the bricks) leaving a solid surface to drive
on that blends with the existing lawn. This now allows
access to the back corner of my lot where I'm putting
up a boat storage building. The seven inches of crushed
rock is rated to handle a load of over 125 psi so I
can park my diesel pusher RV in the back also. The final
'test' came when a concrete truck (loaded with 8 yards
of concrete) backed in. My work passed with 'flying
colors' as there are no settled bricks and no cracks
at all.
|
 |
I
feel I met my goal of retaining the original look of my lawn
as I did not want more concrete across the front yard. By
the way, every one of those 'sod plugs' was cut and planted
by hand (with a homemade plug cutter). I'm building this entire
turbine powered boat project (start to finish) the same way-
with determination and my bare hands. I certainly can't work
at the same pace I did when I was younger, but I still make
steady progress. It's definitely not a "gimme from Daddy".
Nor did I just "write a check". Nobody can say I
don't work hard toward my goals.
Breaking
ground for my Boat House
Here's
what it looked like when I started. I spliced three photos
together in Photoshop to show the 'panoramic view' across
the back corner of my lot.
 |
The
kids outgrew the 'tree fort' we had in the apple tree
(so I removed it and the double stainless steel slide).
The transparent apple harvests had dwindled in recent
years (and the trunk was full of rot) so it was a good
time to remove it. I'll likely plant a semi-dwarf 'Swedish
Apple' to replace it after all the construction is done.
|
I
gave the apple wood to a local guy who uses it to smoke
his own meats and the stainless slide went to another
family where it will provide years of joy for their
kids (just like it did for my kids). I removed a few
trees to clear the area and surprisingly, the 6"
diameter prune tree stump gave me more trouble than
the 36" diameter apple tree- figure that.
|
 |
 |
I built a raised garden area out of railroad ties for
my lovely wife and relocated her plants from the old
garden area.
My
neighbor brought his 'digger' over and cleared my building
site. Now I can lay out the perimeter, locate the posts
and dig some holes.
|
 |
My
plans came back from the designer requiring 10" holes
dug 4 feet deep (for the 6 by 6 posts). So I bought a two-man
gas auger and ordered 20 foot pressure-treated 6 by 6 posts.
Then, when my plans got 'blessed' by the Engineer, suddenly
they are redrawn requiring 30" holes dug 5 feet deep.
No 'heads up' we modified the holes, no 'oh by the way' we
changed the plans. Suddenly my gas auger is too small, and
my posts too short. Doesn't anybody communicate?
 |
The
folks over at NC
Machinery were very helpful. They set me up with
a 'Monster Auger' and I was able to get all my holes
bored in just a couple hours. The dirt from the sixteen
holes raised the work area about five inches, so I'll
need to level it all out again after the posts are set
and holes filled.
The
building inspector signed off my setbacks, erosion barrier,
post holes, and gave me the 'all clear' so I can continue
on. He was much more cooperative (and knowledgeable)
than the other Building Inspector I worked with previously.
|
 |
Setting
up the foundation for my Pole Building Boat House
A
"Pole Building" uses a method of construction where the weight
of the building is supported by the posts, not by a foundation
(as in a conventional 'stud framed' construction). The Pole
Building or Pole Barn method of construction is popular
for agricultural buildings and usually includes a sheet metal
exterior.
These
22 foot 6 by 6 posts only weigh a couple hundred pounds each,
but are very awkward to handle. I put my electric hoist atop
two sections of scaffolding (mounted on my utility trailer)
and with the help of my Son, was able to maneuver each post
into place.
 |
My
building has two ten foot bays and two twelve foot bays,
plus I added two posts ("A" and "B"
in the photo on the left) to support the end of two
overhead steel I-beams. On each of the steel I-beams
I'll hang a 1-ton overhead hoist (on a trolley) that
will allow me to lift my hull for rework, pull my motor,
or complete my other lifting needs.
Here's
the I-beams I'll use for my overhead hoists. They came
from the demolition of a local mall (currently undergoing
a remodel) and were used to support the roof over an
ice rink. I 'cleaned up' the lower flange with my grinder
and got my hoist trolley adjusted to fit, so they'll
work just fine. I'll fabricate brackets so the ends
will bolt to the tops of my 6 by 6 support posts.
|
 |
 |
I
located the bottom of the 16 post holes with my laser
level (and a long stick) then poured redi-mix
concrete 'pads' for my posts to set on.
With
all the posts set in place, I used my laser level to
ensure they are vertical. My laser shines a line about
ten feet long (along the edge of the post) and I'm able
to get it exactly plumb; pretty slick! Way more accurate
than a bubble level.
|
 |
 |
I
double checked all my measurements, and added braces
to hold the posts in place. The inspector 'eyeballed'
the posts for proper clearance (sitting in the empty
holes), and gave me a 'thumbs up'. Now on to the next
step.
I got the concrete truck to bring a couple loads by
and fill in the post holes. Loaded with 8 yards of concrete,
it was a good 'load test' for my 'turfstone' driveway
(at the top of this page). Passing with 'flying colors'
there are no settled bricks and no cracks! What a relief.
|
 |
 |
Now
that all the post holes are filled I can get prepared
for pouring the concrete slab.
I'll
spread this load of sand as a level base for my slab
to rest on and set the posts for my 'walk in' door.
|
 |
 |
To
the 'untrained eye' this may not look like much, but
this represents a couple hard days work; leveling, smoothing,
and packing with my gas powered "jumping
jack" Wacker packer.
Here
we've got the vapor barrier all spread out and 'tie
bars' installed on the posts and form boards (to tie
it all together), just waiting for a pair of concrete
trucks to show up in the morning.
|
 |
 |
After
a 'parade' of concrete trucks dumped their loads, my
slab is finally in.
These
professionals make it look easy.
|
 |
 |
I
used a "5-sack" concrete mix with Fibermesh
and added a couple inches (thicker than code) to ensure
it will handle all future heavy loads.
The
experts put on the finishing touches. The result is
a beautiful, polished finish that looks as smooth as
an ice rink.
|
 |
Now
that we're done 'digging in the dirt', it's time to get this
Boat House framed up
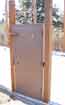 |
I
salvaged two steel I-beams and a nice pre-hung, steel
fire door from the demolition of a local mall. I located
a new hydraulic closer and high-security lockset that
I'll install after the door gets painted.
With
a solid floor in place, my scaffolding easily rolls
around so I can work the walls and overhead a section
at a time.
|
 |
 |
In
preparation for having the trusses delivered, I mounted
2x6 brackets atop the posts (bolted on with heat-treated
3/4" bolts as required). The trusses will sit on
these, lagged to the post and blocked together in pairs
(for rigidity). I was able to locate enough 'monster
bolts' at Pacific
Industrial Supply in Seattle to do the job. If you
stop by, make sure you give yourself enough time to
explore the entire yard- they've got all kinds of cool
'surplus shipyard stuff' stashed everywhere. Very interesting.
I
fabricated brackets on the ends on my steel I-Beams
to bolt into the support posts. To transport around
to the boathouse, I backed my boat trailer over them
and chained them to the underside of the frame. After
parking on the boathouse slab, I lowered them onto carts
and wheeled into position for the crane to lift atop
the posts.
|
 |
The
'truss guy' set my two steel I-beams and all the trusses in
place for me. I lagged them all to the posts, installed the
'eve boards' along the ends of the trusses (to support the
edge where the wall meets the roof sheeting) and blocked the
tops of the trusses.
 |
Lot's
of two by sixes nailed between the posts will support
the sheet metal exterior skin. In this front view (on
the left) you can see where I framed the top of the
doorway to support the rollup door track and springs.
I've got 14 feet of clearance through the door and under
the I-beams.
I
made an extension on the top of my scaffolding to support
my 24' Stinson
plank. It allows me to reach the top of the trusses and just clears under the steel I-beams (so I can roll it anywhere inside the building). The purlins
went up pretty fast as I didn't have to do any fitting;
they just overlap (screwed together and screwed into
the trusses).
|
 |
The building has 'stiffened up' and feels a lot more rigid
(when I'm climbing around on top) now that it's all framed in and bolted together.
Wrapping
up the exterior: with the metal sheeting on it should look
more like a Boathouse
I
selected 29 gauge Nor-Clad
XL metal panels by ASC
Building Products to keep the weather out. The lifetime
warranty will help keep future maintenance to a minimum. I
selected colors to blend with the existing walls and roof
of my house.
 |
After
trimming the doors and bottom edge, the wall panels
went on over a layer of Tyvek
Housewrap (to act as a vapor barrier).
The
16 foot sheets weren't too bad, but it was a little
'hairy' getting those 20 foot sheets up into position
on the end wall (especially when the wind picked up).
I was able to 'walk' one end up the ladder then carry
the sheet vertically into position (looking up to keep
it balanced). Now all four walls are sheeted and the
corners are on.
|
 |
 |
I got all the hurricane ties installed (to anchor the
purlins securely to the trusses) and installed ceiling
supports down the centerline (so I can stand and reach
to attach the roof sheets). The roof panels also go
on over a layer of Tyvek Housewrap. A layer of Radiant
Barrier will go across the inside of the ceiling
joists to help reduce the heat buildup during the summer
months.
The
side door looks a lot better with paint and trim. I
installed a couple Roof
Anchors (attachment loops for my safety harness)
so I can walk around without fear of doing a 'belly
flop' off the roof.
|
 |
 |
I made a jig to hold the first couple sheets in position
(with a 2 inch overhang) and to ensure the row starts
straight. With over 75 screws in each roof panel, it
takes time to properly fasten.
I
started at the front and worked my way toward the rear.
The weatherman has been very cooperative; this Summer
and Fall has been unusually dry.
|
 |
 |
The
trusses are 4:12 pitch so there's not much wasted space
above the ceiling.
I'm
all done with the exterior sheet metal and passed the
Building Inspector's final inspection with 'flying colors'.
|
 |
 |
I'm
satisfied with how my steel fire door turned out. I'll
install my deadbolt next, then add weather stripping
all around before I start heating.
Putting
up my 16 foot wide by 14 foot high insulated, overhead
door was the last step to make this building 'weather
tight'. At least the door is now sitting in place (sealed
with weather-strip) so I don't care if it rains, snows,
or blows here all winter long. After an unusually dry
summer, we can certainly use the rain.
|
 |
 |
I
took advantage of another sun break and cleaned up the
back yard. With most of my lumber used up, I stacked
the remainder inside and finally got rid of that ugly
white tent.
It will be nice have a 'usable' backyard again.
I
screened some of the dirt that came out of the ditch,
leveled the area where the tent was, and replanted grass.
The grass should fill in over the next few weeks.
|
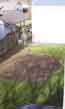 |
Finishing
the interior of my Boathouse
Now
that my outside is done, it's on to finish the interior.
 |
I
got the overhead door track installed and adjusted (it's
nice to be able to open the door when I need to).
Tackling
the 'not so exciting' job of framing the interior means
fitting lots of 2 by 6's across the ceiling and in the
walls.
|
 |
 |
I
setup some temporary lighting, installed my one ton
hoists, added long cords, and set the limit switches
(to properly halt travel at both ends of the chain).
Now both 1-ton hoists are operational.
Finally;
all the walls are framed up. Now I can move on to the
wiring.
|
 |
I
took a short break to set up a pair of Rolls
Royce Gnome turbines for ground running.
 |
I'm
glad my building is 'sealed up' now that 'Old Man Winter'
is here.
|
 |
I know I'm making progress, but seems like there are
still a thousand things to get done before I can even begin
working on my boat. Ugh!
|
 |
 |
I
got some R-19 insulation installed in the side walls.
The lower area is left open so I can string wires. All
my 'stuff' is on wheels, so I can roll it around to
work each area.
A
came across a nice Consew
206RB-3
sewing machine. Equipped with a walking foot, it will
handle my upholstery tasks with ease. I know I'm a little
ahead of myself, but this is one piece of gear no boat
shop should be without.
|
 |
I
took another break to attend the Vacuum Infusion Course at
the local community college so I could
repair the transom on my race boat.
 |
I'm
done pulling the interior wires. My building features
a 50A welder outlet, two 20A 220v circuits for my large
woodworking tools as well as lots of 120v outlets on
several separate circuits scattered all around the building.
My
new Dayton 60,000 BTU natural gas overhead heater is now hung and properly vented
so I'll be able to 'kick the heat up' to fiberglass,
or wrench anytime, year-round.
|
 |
Now
that the Electrical Inspector has completed the 'cover inspection',
we'll put up the remaining R-19 wall insulation, then the
radiant barrier will go up. Then I'll need to hang about 98
sheets of 5/8" wallboard to finish the interior- Ugh!
Then mud and paint.
I
fabricated a drywall cart with a set of monster casters I
had stashed away. With the cart chained onto my flatbed trailer,
I had the forklift driver at the 'big box home improvement
store' set the entire stack of Gypsum right on my cart. Once
I got home, I backed under my overhead hoist and lifted the
entire cart. This way I don't have to re-stack drywall several
times. Besides, no matter where I put the stack, it would
be in the way. This way the entire stack is easily moved just
by shoving the cart around.
 |
With
the R-19 wall insulation put in the walls, I moved all
my junk over to one side so I can sheetrock half the
building at a time. I've stapled radiant barrier onto
the back of each sheet of drywall, so it goes up pretty
slick (and will prevent the interior of the building
from roasting when the summer heat bakes the outside
of the metal sheets).
My
drywall lift helps, but it's still pretty slow going.
Lot's of trips up and down the ladder.
|
 |
 |
I
don't know if the second stack will be easier because
I'm 'already warmed up', or will be more difficult since
I know 'what I'm up against'.
Half
the interior is now covered with gypsum wallboard; I
just need to add the corner trim.
|
 |
 |
A
little light tan latex paint makes it look pretty respectable
on the one side. I've moved all my junk over into this
finished half and have started to work the other side.
My
utilities are laid between my buildings; electrical
power, cable TV, natural gas, phone, fire alarm, intruder
alarm, Internet, and compressed air (from my compressor
in the shop). The trench has been back-filled, leveled,
and packed down with my gas powered 'jumping jack'.
I think I'll lay stepping stones as a walking path between
my buildings. I'll do the final leveling and set the
stones when the weather clears up again.
|
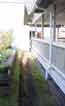 |
 |
I
scored a 'boat load' of high-output,
energy efficient light assemblies from a local 'big
box' grocery store undergoing remodel.
After the individual light units are wired in parallel
and riveted together into rows, they will be surface
mounted across the ceiling. I also had some sheet metal
trim fabricated to hide the rough edges and give them
a 'built in' look.
|
 |
 |
I've
been working inside (on days when the weather is nasty)
and have put up all the insulation and drywall on the
second half.
96
sheets of drywall were put up (two left over). Mudding
and sanding is done.
|
 |
 |
I
blew the overhead to R-32 with 54 bags of cellulose
insulation.
|
 |
 |
The
'concrete guy' came and put in my rear walkways. He
makes the work look easy and did a beautiful job.
I
called and got the final electrical inspection done.
I had to wait till the walkway was in as the power feeder
must be covered with concrete when it's less than 24"
from the surface. Now the landscaping is finally all
done and my boathouse is ready to work.
|
 |
My
Boathouse is almost done!
 |
I've
been looking forward to this day for a long time and
seeing these finished walls is a big morale booster
for me. At this point I'm only a few small steps away
from completion then I'll be able to work indoors, anytime,
in any weather on the conversion of my turbine powered
boat.
It is essential that I have a well lit, energy-efficient
building as much of my remaining boat repair work (applying
epoxy resin and polyurethane finishes) must be done
in a climate controlled area.
|
 |
 |
I
cleaned up the area I had previously trenched for the
utilities hookup. The brown conduit on the far right
provides power to my boathouse. After a quick trip to
Cascade
Stone Supply for some landscaping materials, I was
able to get that area looking pretty good.
My
pallet rack and work bench are setup so my boathouse
is finally getting that 'lived in' look. My Stanley
Vidmar cabinets fit nicely along the wall storing
my stainless fasteners, boat and aircraft parts with
little wasted space. With all five rows of Compact Florescent
Lights now installed, they output about 5.3 ga-jillion
candlepower and draw less than 14 amps total. Priceless.
|
 |
 |
My
30 foot Cobra Terminator Cat is inside now, safe and
sound. I've started to fill
the transom in preparation for final finish.
As
I make progress I'll add content to the bottom of the
Turbine
Boat page.
|
 |
 |
I
setup my straps, rigging, and hoists for a 'lift test'
and confirmed that I can indeed lift my hull. As part
of my ongoing hull preparations, I'll be completing
a couple small composite repairs to the bottom, then
giving it a fresh coat of 'Sun Yellow' AwlGrip 2 Polyurethane
topcoat.
When
I get done this race boat will look like its going 120
mph when it's still sitting in the parking lot!
|
 |
Here's
a Virtual
Tour of my Boathouse.
The
next 'hundred miles'
Now
that I'm out of the 'boathouse building business' I can focus
full time on my turbine powered boat project. First up are
some of the 'not so exciting' tasks such as sanding, filling,
and painting. (UGH)
Since
I already repaired
my transom during the Vacuum
Infused Plastics (VIP) Course at Skagit
Valley College I'm using epoxy resin mixed with 3M
Glass Bubbles to fill, then board sand, apply primer,
then shoot a topcoat of polyurethane. I've got all the deck
hardware removed, so I'll also apply a new topcoat finish
on the remainder of my hull. Then, with fresh paint and all
new stainless steel deck fittings I'll have (essentially)
a brand new hull to start my turbine conversion with. Then
I'll install my Arneson
ASD8 surface drive on the transom and work my way forward
to locate the mounting position of my T58-GE-8F
turbine. I'll infuse some "T" shaped Carbon
Fiber composite brackets in place on the side of the hull
and stringers to support the lube oil tanks, batteries, hydraulic
pumps, fuel filters, etc. Then, after the interior gets a
fresh topcoat, it will be time for plumbing, wiring, carpeting,
and seating.
If
all goes as planned, I hope to be testing on the water in
time for the upcoming boating season. I've already been working
on this project four years now and am not about to 'rush through'
anything. Safety is paramount and I want everything done correctly.
I'm
sure this rig will turn some heads as turbine boats are pretty
rare up here in the north Puget Sound area.
My
boat repairs continue on the Composite Repair page.
My
turbine
powered boat is now complete.
"It's
gonna rip!"
|